Custom Designed HRV
This system was installed a few years ago as a prototype.
We sell a great little air to air heat exchanger for welding shops called "Keep The Heat".
Their only real drawback is that they only make one size of unit that exhausts about 1500 CFM.
If a customer needs more air flow they just add more units to achieve the desired total.
We ran into a few jobs where the customer simply didn't have enough room to install the required number of systems.
We sat down and we designed a large system that we were pretty sure would work and we sat on it for a while. One day a local welding shop owner came into the shop to talk to me and he was one of these people. He needed 6 systems but the design of his building would not allow for it. I told him about our idea and he simply said "Let's try it!"
Now seeing as this was about a $90,000.00 gamble on a theory. We were really excited....and nervous as hell.
The system took about 6 weeks to fabricate and install and actually exceeded our expectations in every way.
The system moves 9200 CFM, is as close to silent as you can get and the ventilation effect was absolutely fantastic. With an outdoor ambient temperature of -10F and a ceiling temperature of 60 degrees F, we were supply fresh air back to the building anywhere from 52 to 56 degrees. (No additional heat source other than heat exchange from the exhaust)
To say the customer was happy is an extreme understatement.
2 years later he built a brand new building 3 times the size. He called me up and said "lets get 3 systems into the new building please".
We have now installed 5 ½ systems and all are working great. (Towards the end of that project this customer sold his 3rd unit to another welding shop that needed something fast. so we have 2 systems fully installed in his building and a 3rd half done.)
The air handlers in these pictures were built by my brother and I in our shop. We have since designed a new air handler with the first customer that they build for us.
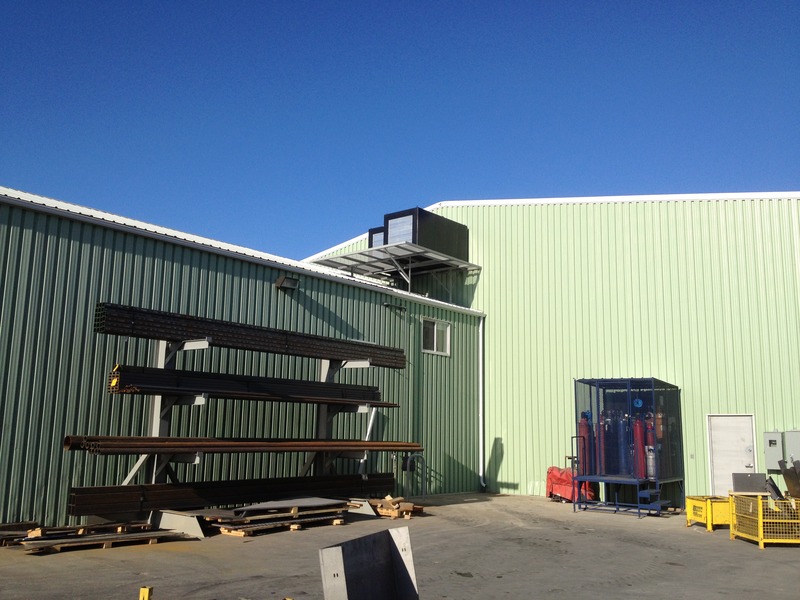
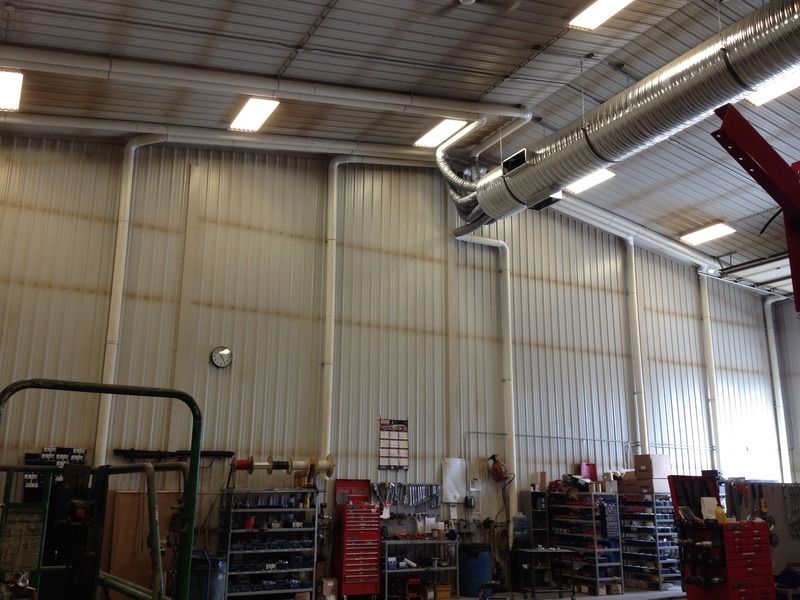
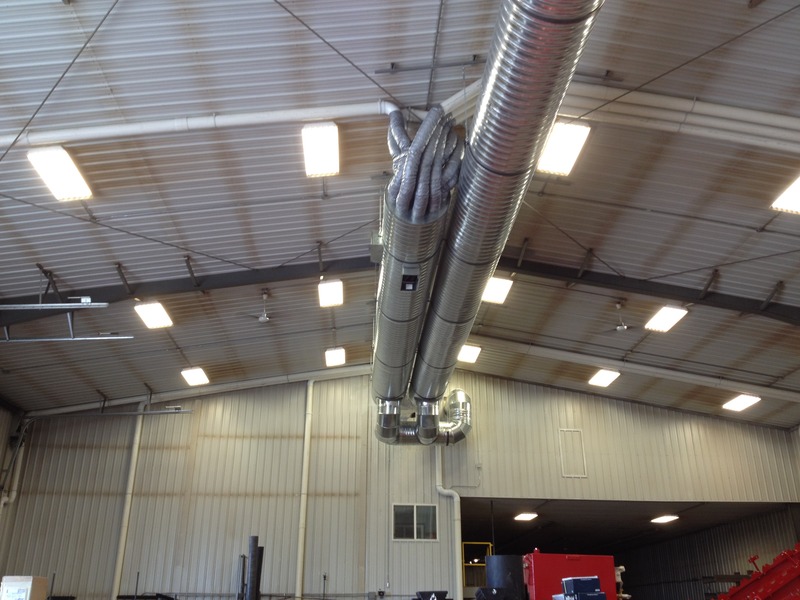
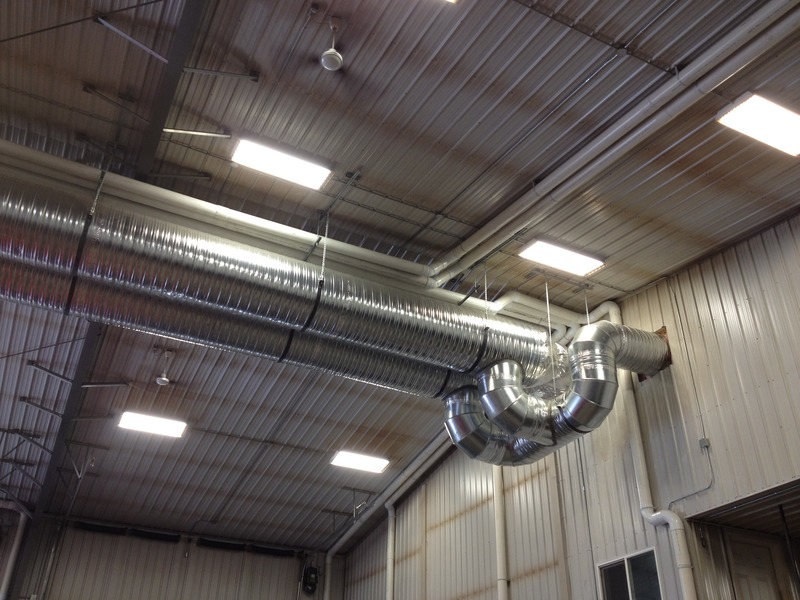
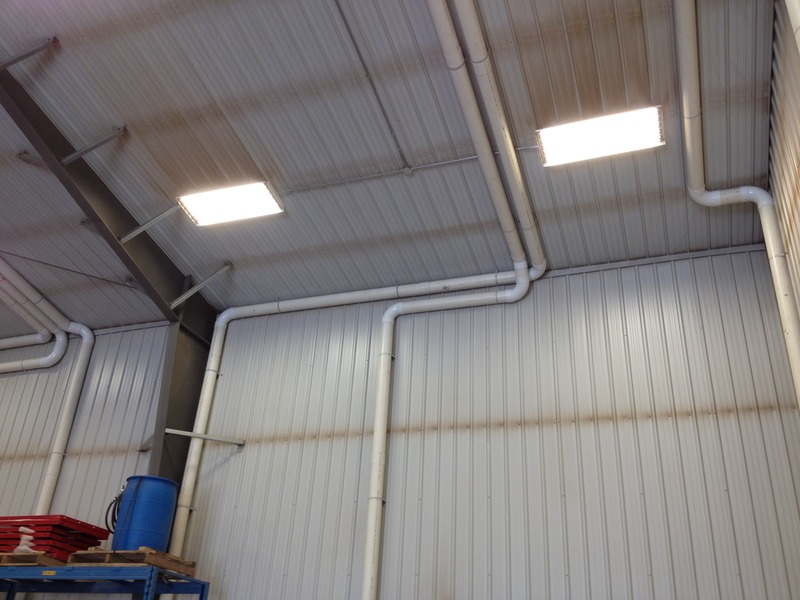
We use 6" Sch 20 PVC for our supply air drops. Believe it or not we actually get a bit of heat "reclaim" from the ceiling using that. We get about a 2 deg rise in air temp from the outlet of the actual exchanger to our air outlets.
|